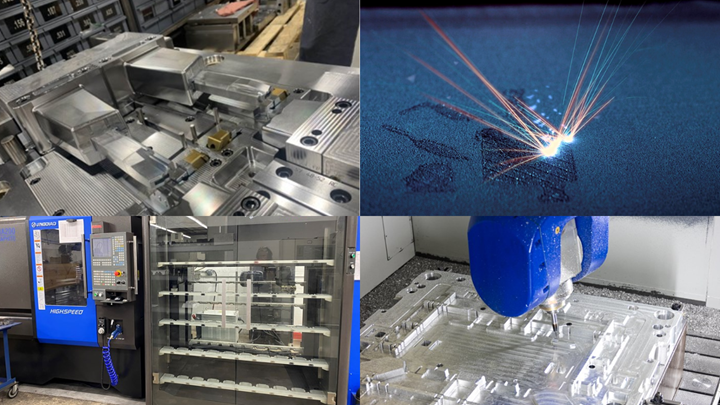
Photo Credit: Zero Tolerance LLC (top left), EOS GmbH (top right), Jingdiao North America Inc. (bottom left) and CDM Tool & Mfg. Co. (bottom right)
MoldMaking Technology publishes monthly case studies that offer detailed insights into the real-world application of various technologies and solutions in the moldmaking industry. Each case study typically follows a format that presents:
- A problem: The specific challenge or issue faced by a moldmaking shop.
- A solution: The technology, process, or strategy implemented to address the problem.
- The results: The impact and benefits achieved by implementing the solution, including quantifiable metrics like cost savings, reduced lead times, improved quality, etc.
Take a look at our most-viewed case studies from 2023 — perhaps one of these problems may resonate with your own shop:
Featured Content
5. Five-Axis Vertical Mill Increases Mold Shop Capacity by Reducing Setups
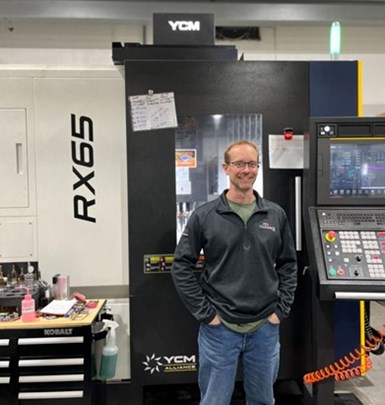
Photo Credit: Zero Tolerance LLC
Zero Tolerance LLC, founded in Kansas in 2011 and later moved to Michigan, specializes in creating molds and injection molding services. In its pursuit of growth while constrained by limited space and budget, the company is strategically expanding capacity. In 2021, it sought a new five-axis CNC mill to enhance capabilities, aiming for versatility, precision, and the ability to work with larger blocks essential for mold production. In short, Zero Tolerance wanted a machine that could do it all while still being compact enough to fit in limited floor space. Read the full article.
3. Five-Axis Graphite Mill With Automation Debottlenecks Electrode Machining
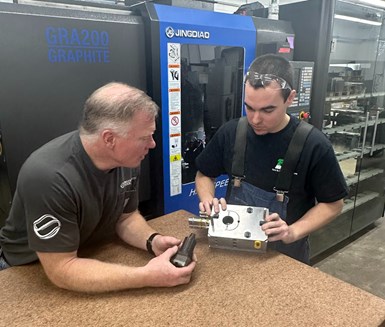
Photo Credit:Jingdiao North America Inc.
Preferred Tool of Hugo, Minnesota, a full-service mold builder, was facing a bottleneck in electrode cutting that was slowing down mold production and reducing shop productivity. To address this issue, the company invested in a purpose-built five-axis graphite mill from Jingdiao with an automation package. The results were impressive: the mill cut electrodes faster with greater detail, reducing setups, cutting and burning time, material use and electrodes needed per job. The mill was installed in April 2022 and has been running at high spindle speeds of 32,000 rpm, as graphite is brittle, not hard, and high-speed machining produces better results with small cutting tools. Read the full article.
1. CAM Automation Increases Mold Production, Quality
At Machining Technology in Brooklyn Park, Minnesota, the programming team in the mold department had been proficiently relying on a CAM software package for many years. However, fresh programming approaches appeared too advantageous to overlook.
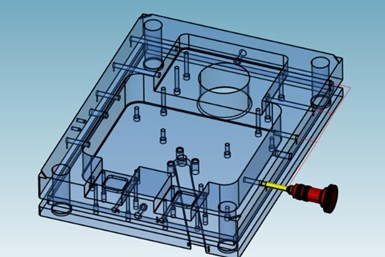
Upon joining Machining Technology as vice president, Miguel Aponte aimed to enhance the mold department's efficiency and quality. Evaluating various areas like processing times and part quality, he targeted a change in CAM software, singling out hyperMILL from Open Mind Technologies. Initially met with skepticism due to established programming habits, the team’s transition to hyperMILL ultimately proved worthwhile, revealing substantial benefits without requiring a leap of faith. Read the full article.
RELATED CONTENT
-
CAM Automation Increases Mold Production, Quality
Mold builder switches CAM software package after 20 years to take advantage of innovative programming strategies that reduce mold machining programming and processing times.
-
VIDEO: CAD/CAM with the Moldmaker in Mind
Ralph Picklo, Director of Sales for Cimatron at CAMBRIO, shares what it means when CAD/CAM is created with the mold builder in mind.
-
Five-Axis Machine With Pallet Changer, 16k-Spindle, Versatile Control Makes More Accurate Molds Faster
The move from three- to five-axis machining with automation reduced setup times and improved surface finishes for this small but mighty Amish mold builder.